Prices / Buy Systems Write A Request
Software Download Technical Support
Inventory Management Systems: An Introduction
Inventory Management Systems (IMS) are the tools and processes businesses use to track their stock levels, orders, sales, and deliveries in real time. Effective inventory management is critical across all industries – from retail and manufacturing to healthcare and food service – because inventory is often one of a company’s most valuable assets. Having too little stock can lead to lost sales or downtime, while holding too much can tie up capital and risk spoilage, theft, or obsolescence. For these reasons, inventory management is important for businesses of any size. Small businesses might start with manual tracking or spreadsheets, but as operations grow, companies turn to dedicated software and technologies (often part of ERP systems) to maintain accurate, real-time inventory records. In short, a good IMS ensures the right products are available at the right time, in the right quantity – improving operational efficiency and customer satisfaction.
We provide Lifetime Software License
No Subscriptions, No Monthly Fees!
Types of Inventory Management Technologies
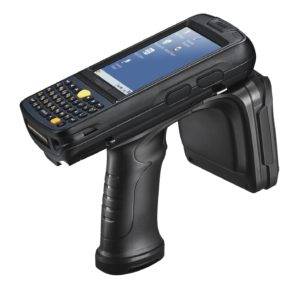
Modern IMS solutions leverage various technologies to streamline tracking and reduce human error. Key inventory management technologies include:
- Manual or Spreadsheet Systems: Smaller operations sometimes rely on physical stock counts or spreadsheets. While simple, these methods are labor-intensive and prone to error as inventory scales.
- Barcode-Based Systems: A widely used technology where each item or SKU is assigned a barcode (typically a printed label with a pattern of lines or a QR code). Warehouse staff or point-of-sale systems use optical scanners (or even smartphone cameras) to read these barcodes and update inventory counts. Barcodes offer a fast and accurate way to input item data, but they require manual scanning of each item and line-of-sight visibility to the code.
- RFID Systems: An advanced system using radio-frequency identification tags on inventory items. RFID tags contain tiny radio transmitters or chips that store item data. Fixed or handheld RFID readers use radio waves to automatically identify items without requiring direct line of sight, even reading multiple tags simultaneously. This technology enables highly automated, real-time tracking of inventory movements.
Other emerging technologies that complement inventory management include IoT sensors (for example, smart shelves that detect stock levels), automated identification and data capture (AIDC) devices, and inventory management software that integrates all data for analysis and forecasting. However, in this article we will focus on the two most prevalent automated identification technologies in inventory management: barcodes and RFID.
Barcode Inventory Systems
Barcodes have been a cornerstone of inventory tracking for decades. A barcode is a machine-readable representation of data; the most common format is a series of printed black and white lines (or a 2D pattern like a QR code) that encode an item number. To use barcodes, each product or SKU is labeled with a unique code. A barcode scanner emits a beam of light and measures the reflected light from the barcode’s pattern. A sensor and decoder then translate that pattern into the corresponding item code, which is logged in the inventory system.
How it works: In practice, when inventory is received, moved, or sold, staff must scan the barcode label on each item or box. This updates the central database with the item’s status (e.g., “added to stock” or “sold”). Barcodes are popular because they are inexpensive and easy to use – printing labels costs pennies, and many items already come with manufacturer barcodes (like UPCs) pre-printed. Additionally, virtually any smartphone or simple handheld scanner can read barcodes, so implementation is straightforward.
Limitations: Barcodes do have drawbacks. Scanners require line-of-sight and can only read one barcode at a time. This means employees must manually aim and scan each item, which can be time-consuming for large inventories. If a barcode label is obscured, damaged, or missing, the item may be skipped or require manual data entry. Also, typically all identical items share the same barcode (e.g. every size M blue shirt has the same SKU code), which makes it hard to differentiate individual units – a problem for tracking unique items or serial numbers. Despite these challenges, barcode systems remain a tried-and-true, cost-effective solution for many businesses, providing accuracy and control with minimal investment.
Prices / Buy Systems Write A Request
Software Download Technical Support
RFID Inventory Systems
RFID stands for Radio-Frequency Identification, a technology that uses electromagnetic fields to automatically identify and track tags attached to objects. An RFID inventory system consists of tags, readers, and a software backend. Each RFID tag contains a tiny radio chip (transponder) attached to an antenna. This tag stores a unique identifier or even small datasets about the item. RFID readers emit radio waves via an antenna; when an RFID tag comes into the antenna’s field, the tag’s antenna powers the chip (for passive tags) and sends data back via radio signal.
We provide Lifetime Software License
No Subscriptions, No Monthly Fees!
How it works: In an inventory context, items are tagged with RFID labels (which can be embedded in product packaging or attached as stickers). As inventory moves in or out of a stock room, passes through a doorway, or is scanned with a handheld reader, the system automatically logs those items. Unlike barcodes, RFID does not require direct line of sight – a reader can scan tags through packaging or from a distance. It’s possible to read dozens or even hundreds of tags within seconds, greatly speeding up stock counts and transaction processing. For example, an RFID handheld can scan an entire shelf of products in one sweep, whereas a barcode scanner would require picking up each item one by one.
Benefits and uses: RFID technology offers real-time visibility into inventory. It can sense when an item leaves a warehouse or store (useful for theft prevention and automated check-out), and each item can have a unique identifier (even if products are identical) for granular tracking. Many industries have adopted RFID for high-value or high-volume inventory tracking – retailers use it for fast inventory audits and to reduce out-of-stocks, manufacturers use it to track parts through production, and healthcare uses RFID to track medical equipment and supplies. Modern RFID systems (especially UHF tags) have a read range of several feet to many yards, allowing entire pallets or store sections to be scanned quickly.
Limitations: The main barriers to RFID adoption have been cost and complexity. RFID tags are still more expensive than printed barcodes – passive tags might cost $0.10 or more each in bulk, and specialized active tags (with batteries) can cost several dollars. RFID readers are also much pricier than barcode scanners (often 10x the cost) and require infrastructure setup. Integration can be challenging as well; ensuring the RFID system’s data feeds correctly into inventory software may require significant IT work. Additionally, RFID signals can be finicky: materials like metal or liquids can interfere with radio waves, causing read errors in certain environments. Despite these challenges, RFID is rapidly growing in use because its efficiency and automation capabilities often outweigh the downsides, especially as technology costs come down.
Prices / Buy Systems Write A Request
Software Download Technical Support
RFID vs. Barcode: Key Differences
Both RFID and barcoding serve the same fundamental purpose – identifying inventory items – but they operate very differently. The table below highlights key differences between the two technologies, and why RFID is often considered a more advanced solution:
Factor | RFID (Radio-Frequency ID) | Barcode |
---|---|---|
Scanning Method | Radio waves; no line-of-sight needed. Readers can scan tags through packaging or from a distance. | Optical (laser/imager); requires direct line-of-sight to read the printed code. |
Bulk Reading | Can read multiple tags simultaneously (100+ tags in seconds), ideal for rapid stock counts. | Can only scan one code at a time, requiring manual repetition for each item. |
Data Storage | Tag can store data (unique ID and other info) and can be read/write (data can be updated). Each item typically has a unique tag ID. | Code typically just encodes an identifier (e.g., product number); additional info resides in a database. All items of a type often share the same code (not unique per item). |
Range | Read range from a few centimeters up to several meters (especially with UHF RFID). Useful for scanning items from a distance or as they move through doorways. | Very short range – typically a few inches to a couple of feet at most for handheld scanners. Each item must be brought close to the scanner. |
Line of Sight | Not required. Tags can be read through obstacles (boxes, clothing racks), and even if hidden from view. | Required. The scanner must have an unobstructed view of the barcode. Dirt, damage, or misalignment can prevent reads. |
Scanning Speed | Extremely fast for large volumes – can scan an entire pallet or shelf near-instantly, significantly reducing labor time for inventory counts. | Relatively slow for large volumes – each item is scanned individually, which can be time-consuming for big inventories. |
Durability | Tags are often enclosed in plastic or embedded, making them resistant to dust, moisture, and rough handling. Suitable for outdoor or long-term use (e.g. tracking assets over years). | Printed labels can wear out, fade, or tear over time, especially in harsh environments. They may need replacement if exposed to water, heat, or abrasion frequently. |
Security | Difficult to duplicate or tamper. Tags can be encrypted or password-protected if needed. Because tags aren’t visible, it’s harder for bad actors to know what to target. Also good for anti-theft systems (e.g. retail stores). | Easier to copy or counterfeit – anyone can read the human-visible code or even photocopy a barcode label. Offers minimal security by itself (often paired with other controls). |
Cost per Tag | Higher – passive RFID tags often cost $0.10 or more each (and up to dollars for specialized tags). Also, reusable hard tags (in retail) need retrieval. | Minimal – typically fractions of a cent for a printed barcode label (or virtually $0 if the item already has a manufacturer’s barcode). |
Reader Equipment | RFID readers are expensive (a single reader can cost hundreds to thousands of dollars) and require setup of antennas/portals for coverage. | Barcode scanners are inexpensive (often under $100), and many devices like smartphones or tablets can serve as scanners with a camera. |
Implementation | More complex – requires integration of reader hardware and software, staff training on new devices, and tuning the system to avoid signal issues (especially around metal or dense environments). | Simple – many businesses can deploy a barcode system with off-the-shelf components and minimal training. Barcodes are standardized and universally understood technology. |
Use Cases | Best for large-scale, high-volume operations or where real-time tracking is crucial (warehouses, big retail, manufacturing, asset tracking, etc.). Often used for item-level tracking to improve accuracy and reduce labor. | Best for small to mid-scale operations or those on a tight budget (small retailers, local businesses). Ideal for cases where items can be scanned one by one at point of use (checkouts, shipping). |
Table: Comparison of RFID and Barcode technologies in inventory management. RFID excels in automation and efficiency, while barcodes are simpler and cheaper to implement.
As shown above, RFID offers clear advantages in terms of speed, automation, and data richness. It can capture inventory data much faster and more reliably in bulk operations, which is why it’s often seen as a superior solution for large businesses. A barcode system might struggle to keep up with a warehouse handling millions of items, whereas an RFID system can perform frequent cycle counts with minimal human effort. One study found that traditional retailers have inventory accuracy of only about 60%, but with RFID technology, accuracy levels can exceed 95%, leading to sales increases of 2%–30%. The ability to do more frequent and accurate counts (e.g. inventory audits every few weeks instead of only twice a year) means fewer stockouts and lost sales.
However, it’s important to note that RFID’s superiority comes at a cost. The technology investments can be substantial, and not every business needs that level of sophistication. In the next sections, we’ll look at the benefits and challenges of each system in practice, and some real-world examples of companies leveraging RFID for inventory management.
Benefits and Challenges of RFID vs. Barcode Systems
Adopting either RFID or barcode systems will significantly improve inventory management compared to manual methods. Yet each technology has its own pros and cons to consider:
Benefits of RFID Inventory Systems
- High Efficiency & Speed: RFID can scan many items at once without direct line-of-sight. This massively speeds up inventory counts and item movements. Tasks like full store inventory that once took days can be done in hours or minutes with RFID (e.g., Zara stores cut physical inventory count time by ~85% using RFID).
- Improved Inventory Accuracy: Automation reduces human error. RFID systems update stock levels in real time as items move, leading to accuracy rates above 95% in many deployments. This accuracy helps prevent stock discrepancies and lost items.
- Labor and Cost Savings: By reducing manual scanning, companies need fewer labor hours for inventory handling. One analysis showed that counting 10,000 items with barcodes might cost $150 in labor, but only about $7 with RFID due to speed and automation. Over many transactions, RFID can significantly cut labor costs.
- Enhanced Visibility & Data: Each RFID tag carries a unique identifier, enabling item-level tracking. Businesses can monitor exactly which item (not just which product type) is where. This is valuable for high-value goods or assets, and it supports advanced analytics (like tracking dwell times in a warehouse, or identifying shrinkage points). RFID can even trigger automatic alerts – for example, if an item leaves a facility when it shouldn’t, or to instantly reorder stock when levels get low.
- Durability and Longevity: RFID tags (especially passive ones) are quite durable and can last for years. They withstand outdoor conditions, rough handling, and repeated use better than paper labels. This makes RFID ideal for tracking reusable containers, equipment, or assets over a long lifecycle.
- Security Features: RFID tags are harder to replicate or forge than barcodes. They can also be used as anti-theft devices (many retail security tags now include RFID). Some RFID systems encrypt data or use password-protected tags for sensitive applications, adding a layer of security. Additionally, because RFID doesn’t broadcast visible information, it’s more discreet. (By contrast, anyone can read a barcode if they see it.)
We provide Lifetime Software License
No Subscriptions, No Monthly Fees!
Challenges of RFID Inventory Systems
- High Initial Cost: The investment for RFID is a major hurdle. RFID readers can be 10 times more expensive than barcode scanners, and setting up readers (e.g., at warehouse doors or retail store ceilings) can require significant infrastructure. Tags also add cost per item (even $0.10/tag adds up with millions of units). For small-margin products or small businesses, this may not be immediately justifiable.
- Integration Complexity: Implementing RFID isn’t plug-and-play. It often requires integrating new hardware with existing inventory management software or ERP systems, which can be complex and costly. Staff need training to use handheld RFID devices and to manage exceptions (like resolving duplicate reads or missed reads). Without careful planning, an RFID rollout can be time-consuming and disruptive to operations.
- Environmental Limitations: Certain environments pose challenges for RFID. Metal shelves or containers and liquids can interfere with radio signals, creating blind spots or read errors. For example, a pallet of metal parts or a cooler full of liquids might be harder to read reliably. Specialized tags and careful reader placement can mitigate this, but that adds complexity.
- Tagging All Items: To gain the full benefit, every item (or at least every case/pallet) needs an RFID tag, which may be a logistical effort. Applying or embedding tags, especially in a manufacturing context, can be an added step in the production or packaging process. In some cases, suppliers and partners need to be involved (as seen with retailer supplier mandates for RFID tagging).
- Not Universally Necessary: RFID can be “overkill” for some businesses. If you run a small shop or have a limited inventory that’s easy to count, the ROI of RFID may be too low. In fact, many retailers find that barcode systems are already efficient enough for their needs. Adopting RFID where it’s not really needed could complicate operations with little added benefit.
Benefits of Barcode Systems
- Low Cost and Accessibility: Barcodes are very inexpensive to implement. Printing barcode labels costs next to nothing, and many products come pre-labeled by manufacturers. The equipment is cheap and widespread – employees can even use smartphones to scan, meaning no heavy hardware investment. This makes barcoding feasible for even the smallest businesses and budgets.
- Simplicity and Reliability: The technology behind barcodes is simple and well-proven. Scanning a barcode is quick and straightforward, with a clear “beep” for each successful read. There’s little ambiguity: either the code scans correctly or it doesn’t, which is immediately apparent to the user. Many businesses appreciate that barcoding involves human oversight of each item as it’s scanned, adding a layer of verification (for example, an employee can catch if the wrong item is being scanned).
- Wide Compatibility: Because barcodes are a universal standard, virtually all inventory software and point-of-sale systems support them. Integration of barcode data into databases is seamless – a scanned barcode instantly pulls up the item record. No specialized integration work is usually required beyond maybe configuring the software to recognize your particular codes.
- Immediate Readiness: Most consumer goods already have barcodes (UPC/EAN codes) printed on their packaging. This means a business can often start tracking inventory with no labeling effort at all, simply by scanning existing codes. Even for custom or internal items, generating a unique barcode via software is easy and fast. In contrast, RFID tagging might involve tagging items that didn’t have tags before, which is more work.
- Adequate for Many Needs: For many small and mid-sized companies, scanning barcodes one by one is fast enough. If you’re dealing with tens or hundreds of items at a time (not tens of thousands), the speed difference between RFID and barcode is negligible. Barcodes can dramatically improve accuracy and efficiency compared to manual counts, and that level of improvement may suffice until a business reaches a much larger scale.
Challenges of Barcode Systems
- Manual Labor Intensive: Because each barcode must be individually scanned with line-of-sight, handling large volumes of inventory can be slow. Doing a full stock count in a warehouse or store means hours or days of scanning items one after another. This also ties up staff labor purely for scanning tasks. Scaling up a barcode system often means linearly scaling labor – e.g., twice as many items might require twice as many staff-hours to count – whereas RFID can handle growth more gracefully through automation.
- Line-of-Sight Requirement: Barcodes won’t scan if the label is hidden, bent, or obstructed. Items on high shelves, stacked boxes, or products with packaging that covers the code can be missed unless handled. This can make inventory checks cumbersome as workers must position each item just right to scan. In messy or busy environments, maintaining clear visibility of every barcode can be impractical.
- Label Damage and Decay: Printed barcodes are susceptible to damage. A torn, smudged, or faded label may not scan at all, causing delays as the item is manually identified or relabeled. Environmental factors like moisture, heat, sunlight, or chemicals can degrade labels quickly. While there are durable label materials, typical paper labels have limited life in tough conditions.
- Limited Data & Uniqueness: Standard barcodes (1D codes) only encode a short string (like an item number). They don’t carry extra data like batch numbers or expiration dates – that information must be looked up in a database via the item number. Also, as mentioned, typically all units of a product share the same barcode, so you can’t differentiate one unit from another without implementing serial barcodes (which many businesses don’t do due to complexity). This limits the granularity of tracking; for example, you can’t easily flag that this specific unitis expired or defective just by the barcode alone.
- No Automatic Tracking: Unlike RFID, which can gate-read items as they move, barcodes require a person to actively scan. This means you don’t get real-time automatic updates; inventory data is only as current as the last scan. If someone removes an item from stock without scanning, the system won’t know. There’s also no way for a barcode system to automatically alert you if an item leaves the premises (unless it’s scanned at an exit). In short, barcodes are not ideal for continuous, passive monitoring.
Despite these limitations, barcodes remain a practical and efficient solution for countless businesses. They strike a balance between cost and control, which is why they have not been completely replaced by RFID. In fact, experts note that while RFID offers clear efficiency gains, it’s unlikely to fully replace barcoding anytime soon, as both technologies have their place and advantages.
Prices / Buy Systems Write A Request
Software Download Technical Support
Real-World Case Studies: RFID Inventory Management in Action
To better understand the impact of these technologies, let’s look at several real-world examples where RFID-based inventory management has been successfully implemented across different industries:
- Zara (Fashion Retail): Global fashion retailer Zara (part of Inditex) undertook one of the largest RFID rollouts in retail. By tagging each item of clothing with RFID, Zara revolutionized its in-store inventory counts and shelf replenishment. At one of Zara’s largest stores, an inventory count that used to require 40 employees scanning barcodes for 5 hours was completed by 10 employees in half the time using RFID. This six-fold efficiency boost meant stores could do inventory audits every six weeks instead of every six months, keeping inventory data far more accurate. The RFID system gives Zara staff real-time visibility into stock levels on the floor and in the stockroom. If an item sells, the system immediately notifies staff to replenish it from the back, and triggers reorders from distribution as needed. This has improved product availability and is credited with increasing sales. Inditex’s leadership lauded the RFID project as transformative for customer service and store operations. Zara’s case shows how RFID can dramatically streamline retail inventory and enable fast fashion operations to run smoothly.
- Walmart (Retail Supply Chain): Walmart, the world’s largest retailer, pioneered RFID trials in the early 2000s and in recent years renewed its RFID mandates for suppliers. In 2022, Walmart began requiring suppliers in certain categories (like apparel, electronics, toys, etc.) to affix RFID tags to all products. The goal is to ensure item-level inventory accuracy and improve omni channel capabilities (e.g., fulfilling online orders from stores). Walmart’s vast supply chain can gain efficiency by having incoming products automatically logged and located via RFID. For example, RFID portals can scan entire pallets of merchandise as they arrive at a distribution center or store, verifying contents instantly – something not possible with barcodes alone. Walmart’s push has been driven by proven benefits: studies found RFID could reduce out-of-stock incidents and improve inventory count accuracy significantly, which for a retailer like Walmart translates to better sales and lower labor costs. This case underscores that even with barcodes being standard, industry leaders see enough advantage in RFID to invest heavily and ask their partners to do the same.
- Chipotle (Restaurant/Food Service): It’s not just retail – RFID is also making inroads in the food industry. In 2022, Chipotle Mexican Grill announced a pilot program using RFID to track ingredients from suppliers to stores for improved traceability and inventory control. They applied RFID case labels to packages of ingredients, so that shipments moving to restaurants could be automatically scanned. This transforms what was a manual check-in process into an automated one. According to Chipotle’s Chief Restaurant Officer, “RFID labels transform inventory management into an automatic, digital function that optimizes restaurant operations and gives our support centers access to inventory data in real-time.” In other words, the company can see exactly which ingredients (by lot and batch) are at each restaurant at any moment. This not only helps with efficient stock replenishment, but also enhances food safety – if there’s a recall or quality issue, they can quickly identify which locations received a specific batch. Chipotle’s early results showed improved employee efficiency (less time spent scanning deliveries) and better visibility for management. This case demonstrates RFID’s value in supply chain visibility and safety for the food sector.
- Automotive Manufacturing (Work-in-Process Tracking): Many manufacturing companies use RFID to monitor parts and assemblies through production. For instance, an automotive plant might tag engine components or subassemblies with RFID. As these parts move from one workstation to the next, overhead readers automatically log their progress. This provides up-to-the-minute data on production status and WIP (work-in-process) inventory. A real case is Toyota, which has used RFID to track vehicle bodies on assembly lines, ensuring the right components are available just in time. Another example is Boeing, which has tagged aircraft parts and even toolkits with RFID to manage maintenance inventories. These industrial implementations have led to reductions in missing parts, improved production scheduling (since the system knows exactly what’s on hand), and time saved in searching for items. In such environments, the durability and reusability of RFID tags are a big plus – tags survive the entire assembly process and can even stay on finished products for post-sale tracking.
(The above examples illustrate the versatility of RFID: whether it’s fashion retail, general merchandise, food service, or manufacturing, RFID-based inventory management has delivered measurable gains in efficiency and accuracy.)
Prices / Buy Systems Write A Request
Software Download Technical Support
Conclusion: Choosing the Best Solution for Your Business
Both barcode and RFID systems can greatly enhance inventory management, but the right choice depends on a company’s specific needs, scale, and resources. There is no one-size-fits-all answer – each technology has scenarios where it shines:
- Small Businesses / Low Volume: For small retailers, local warehouses, or businesses just starting out, a barcode-based inventory system is often the best choice. It’s inexpensive, easy to implement, and reliable. You can get up and running in days, and the accuracy improvements over manual tracking are huge. If your inventory can be managed by scanning items individually without excessive labor, barcoding meets all the requirements at a fraction of the cost of RFID.
- Large Enterprises / High Volume: For large-scale operations – think big-box retailers, large e-commerce fulfillment centers, manufacturers with complex supply chains – RFID is usually worth the investment. When you have to keep track of thousands or millions of moving parts and products in real time, the efficiency gains of RFID (bulk scanning, automation, real-time data) outweigh the costs. RFID shines in high-volume, high-velocity environments where even small percentage improvements in accuracy or labor efficiency translate to big dollars saved. Many such companies have found that a properly implemented RFID system pays for itself through labor reduction and improved stock accuracy (preventing lost sales due to stockouts, etc.).
- Mixed Approach: It’s worth noting that some businesses use a hybrid approach. They might use barcodes for certain operations and RFID for others. For example, a retailer could use RFID in their distribution center and for doing periodic inventory counts in stores, but still use barcodes at the point-of-sale for checkout (since customers are already familiar with barcode scanning at registers). Similarly, a manufacturer might use RFID for tracking pallets or containers and barcodes for individual components. The two technologies can coexist and even complement each other.
In summary, RFID is a more advanced solution offering superior speed and automation, ideal for companies that need those capabilities and can justify the cost. Barcodes remain an excellent, budget-friendly solution that is sufficient for many scenarios. The decision should be guided by a careful cost-benefit analysis: evaluate the volume of transactions, the pain points in your current inventory process, the required accuracy, and the available budget. For some, upgrading to RFID will unlock the next level of efficiency and data visibility; for others, optimizing a barcode system or sticking with barcodes will be the prudent choice.
No matter which technology you choose, the end goal is the same: to have a well-organized, accurate inventory management system that keeps your business running smoothly and your customers happy.
FAQ (Frequently Asked Questions)
Q: What is an inventory management system (IMS)?
A: An inventory management system is a combination of software and processes that businesses use to monitor their stock levels, track orders and deliveries, and manage inventory operations. It provides a central record of all items a company has in stock (across warehouses, stores, etc.), usually in real time. A good IMS helps ensure you have the right amount of product available – not so little that you run out (stockouts), and not so much that capital is tied up unnecessarily. It often includes tools for forecasting demand, generating purchase orders when stock is low, and analytics to optimize inventory. In short, it’s the system that keeps tabs on what you have, where it is, and when to replenish it.
Q: How do barcodes and RFID differ in how they work?
A: Barcodes are visual patterns (lines or QR codes) that represent data – typically an item number. To use them, a person must scan each barcode with a reader (like a laser scanner or camera), and the scanner interprets the code to identify the item. This requires line-of-sight and one-at-a-time scanning. RFID uses radio frequency tags that transmit data wirelessly. An RFID reader can detect tags without seeing them – even if they’re inside a box – and can scan many tags at once. In essence, barcodes are like an “eye” that needs to see each label, while RFID is like a “radio” that can hear many tags broadcasting at once. Both ultimately feed item information into the inventory database, but RFID automates much of the capture process that barcoding handles manually.
Q: Is RFID always better than barcodes for inventory management?
A: Not always – it depends on the situation. RFID is technologically superior in many ways (no line-of-sight needed, bulk reading, more data per tag), which can make it much more efficient for large inventories. For example, RFID is great for a warehouse doing full inventory counts or a store that wants real-time tracking of merchandise. However, RFID is also more expensive to implement and may be overkill for a small operation. Barcodes are very cheap and might be “good enough” if your volume is manageable with manual scanning. Many businesses successfully use barcodes and see no need to switch to RFID. Others reach a point where the labor savings and accuracy gains from RFID justify the cost. So, RFID is “better” in capability, but whether it’s better for youcomes down to scale, budget, and needs.
Q: Can I use both RFID and barcodes together?
A: Yes, and many companies do. The two systems aren’t mutually exclusive. You might use barcodes in some parts of your operation and RFID in others. For instance, you could tag pallets or high-value items with RFID for automatic tracking, but still use barcode labels on individual products for compatibility with standard POS systems or shipping labels. Using both can provide redundancy as well – if an RFID tag fails, a barcode on the item could be a backup for scanning. The key is to ensure your inventory software can handle both data inputs, but most modern systems can. A hybrid approach can be a stepping stone: you can gradually introduce RFID in areas where it makes the biggest impact while retaining barcodes elsewhere.
Q: What are the costs involved in switching to an RFID system?
A: The costs for RFID can be broken down into a few categories: tags, hardware, and integration. RFID tags are more expensive than barcode labels – passive tags might be around $0.10 each (in bulk) and specialized tags more. If you have hundreds of thousands of items, tagging them adds up. Then you need RFID readers (handheld units can be several hundred dollars each; fixed readers and antennas for warehouse portals can run into thousands each). Depending on coverage needed, you might require multiple readers. Next is the software/integration cost: your systems need to be configured to accept RFID data. This could involve new inventory management software or updates to existing systems, plus services to set it up. You’ll also have training costs for staff to learn the new equipment. In summary, initial investment for RFID is significant – often tens of thousands of dollars for a small warehouse setup, scaling up from there. It’s wise to conduct a cost-benefit analysis: estimate how much RFID will save in labor, losses, or other efficiencies to see how long it takes to recoup the investment. In contrast, a barcode system’s costs are very low (labels and a few $100 scanners), which is why barcodes are usually the first step for inventory management.
Q: Which industries benefit the most from RFID inventory management?
A: Industries that deal with large volumes of inventory, high-value items, or require high accuracy and speed tend to benefit most from RFID. Retail fashion and apparel have widely adopted RFID – stores like Zara, Nike, Macy’s, and others use it to keep shelf stock accurate and enable omni-channel sales (fulfilling online orders from store inventory). The logistics and warehouse sector also benefits greatly: RFID can automate receiving, picking, and shipping verification in distribution centers. Manufacturing (especially automotive, aerospace, electronics) uses RFID to track parts and improve production flow. Healthcare uses RFID to track medical devices, surgical tools, and even patients’ medications, ensuring critical supplies are always on hand and not expired. Pharmaceuticals may use RFID for pedigree tracking of drugs (to combat counterfeiting and manage recalls). Even libraries and archives use RFID to manage books and files efficiently. Essentially, any industry where inventory accuracy and timing are crucial – and where the volume of items would make manual barcode scanning tedious – is a strong candidate for RFID. Businesses with frequent inventory loss (theft or misplacement) also see value in RFID’s tracking capabilities.
Q: How does an inventory management system improve business performance?
A: An IMS prevents a lot of common problems and adds intelligence to operations. By keeping accurate track of stock, it prevents stockouts (so you don’t miss sales because a product wasn’t on the shelf) and prevents overstock (which ties up cash and might lead to waste). It also reduces the manpower needed for inventory tasks – for instance, automatic tracking (whether via barcodes or RFID) means employees spend less time searching for items or doing manual counts, and more time on productive tasks. With a good IMS, companies can analyze sales trends and seasonality to forecast demand and set optimal reorder points, leading to better demand planning. This often means higher sales (because products are available when customers want them) and lower costs (because you aren’t storing excess or rushing urgent orders). Inventory systems also improve accountability – you know who handled what and when, which can deter internal theft and reveal inefficiencies. In summary, an IMS contributes to higher efficiency, lower operational costs, better cash flow management, and improved customer satisfaction by ensuring the right products are in the right place at the right time.